Surstocks de Walmart : une histoire de Supply Chain
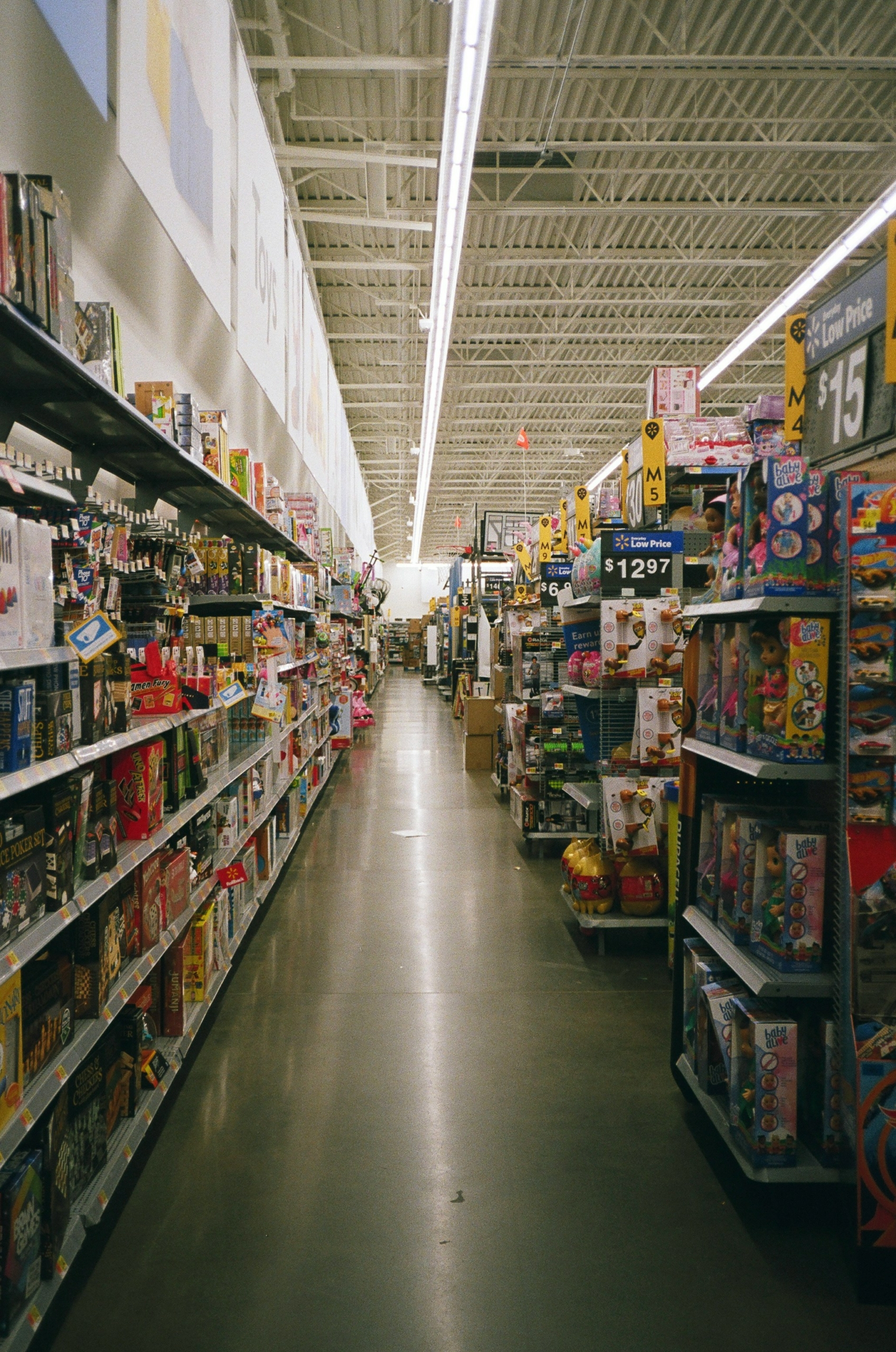
Une information récente ne vous aura peut-être pas échappé. Elle a son importance dans le monde de la distribution. Plusieurs retailers américains, notamment les plus grands comme Macy’s, Target et Walmart, ont vu leur niveau de stock augmenter drastiquement. Les surstocks sont spectaculaires. A la fin du premier trimestre entre 17% et 45% de hausse par rapport à l’an dernier. Le CEO de Walmart a même annoncé que si 20% du stock pouvait disparaître du jour au lendemain, cela serait idéal.
Les causes du surstocks et de l’emballement de la Supply Chain
Nombreuses sont les Supply Chain qui se tendent et se détendent, enchaînant des pics de charge et de sous-charge. Cet effet « coup de fouet », ou « bullwhip effect », est d’autant plus remarquable qu’il peut se dérouler y compris avec des demandes stables et prévisibles. Cette variabilité, engendrée principalement par des décisions et des outils, crée des dysfonctionnements importants dans les entreprises.
COVID et tensions sur les approvisionnements
Le COVID a accentué cet effet. Les décisions initiales ont été de couper beaucoup d’approvisionnements dans la crainte d’un arrêt fort de l’économie et d’appuyer plus fort sur d’autres, notamment les biens de première nécessité. Le redémarrage a également été assez violent avec un rattrapage de grande ampleur. L’exemple des masques est connu de tous. Ils sont en effet rapidement passés du bien le plus précieux de la planète à un élément présent en surabondance. Dans ces conditions, il est très difficile de piloter une Supply Chain.
En parallèle, la complexité a augmenté du côté de l’approvisionnement. Les signaux qui circulent dans nos supply chains sont de plus en plus désynchronisés avec la demande réelle.
Prévision et automatisation des réassorts
Les distributeurs américains vivent donc cette situation. Le redémarrage de leur activité les a incités à projeter une croissance importante de la consommation. Des approvisionnements importants ont été placés sur une durée longue. Malheureusement, la consommation n’a pas suivi et s’est en plus décalé vers d’autres produits. Cela génère des surstocks monumentaux, avec de multiplies impacts : en termes d’organisation en magasin ou en entrepôt, d’immobilisation et de performance financière, de positionnement commercial et d’agilité à renouveler son offre, l’écoulement de ces surstocks passant notamment par des remises importantes à mettre œuvre pour les consommateurs.
Un facteur aggravant intéressant à analyser : le recomplètement des stocks en automatique. Ces points de commande automatiques fonctionnent en effet parfaitement si les prévisions qui ont servi à leur dimensionnement se réalisent. Mais comme ils ne sont pas assez dynamiques, on se retrouve avec du stock qui est appelé alors même qu’il est déjà excédentaire. Le résultat ne trompe pas : les dépôts débordent, ainsi que les allées elles-mêmes des hypermarchés.
Un cycle qui peut se reproduire ?
L’avenir dira si, échaudés par ces problématiques, les approvisionnements seront coupés au point de… générer des ruptures. Nous passerions alors à la phase la plus basse de l’effet coup de fouet. Ceci créerait des pénuries qui pourraient accentuer la demande. La réaction serait alors… de relancer des approvisionnements pour répondre à la demande. Vous connaissez la suite !
Comment anticiper ces problématiques
De nombreuses fois vécues et étudiées, ces perturbations de la Supply Chain peuvent être jugulées. Sans lister la totalité des possibilités, voici quelques pistes particulièrement intéressantes :
- Transformer son modèle du flux poussé vers le flux tiré. Le flux tiré possède l’avantage de s’appuyer sur la consommation réelle. Dans ce cas, la prévision sert à dimensionner des stocks et des points de découplage.
- Travailler à la réduction des délais d’approvisionnement. Ceci a pour avantage de limiter le risque et rendre la Supply Chain plus agile et réactive.
- Mieux travailler avec ses fournisseurs, et lorsque cela est possible, ses clients. Donner de la visibilité en amont et en aval de la chaîne a tendance à réduire les effets de variabilité. Ainsi, un fournisseur qui travaille en VMI (gestion partagée des approvisionnements) et qui a la visibilité sur le stock de son client aura plus de visibilité pour lui permettre d’amortir les à-coups.
- Traiter de façon différenciée les articles selon une segmentation adaptée. Cette segmentation peut être selon la classe ABC/XYZ, les délais d’approvisionnements ou encore la fiabilité fournisseur. L’avantage consiste surtout à identifier des modes de fonctionnements différenciés par catégorie pour gagner du temps et de la performance.
- Prendre du recul sur des outils intégrant des règles de plus en plus riches. Dans notre monde de plus en plus variable et imprévisible, la volonté de coupler l’ensemble des outils de l’aval de la chaîne jusqu’à l’amont peut avoir tendance à accentuer la variabilité. Les calculs sont optimisables sans avoir d’impact sur la performance globale.
- S’assurer d’une bonne appropriation des processus par les équipes, pour une adéquation entre ce que permet l’outil, son paramétrage et son utilisation pour l’exécution de l’approvisionnement au quotidien
Ces différentes pistes permettent d’adresser la réduction du stock inutile (et des surstocks). Elles permettent également d’améliorer la disponibilité produit, l’objectif étant de disposer du bon stock au bon endroit.
Nous pouvons noter que certains de ces principes sont les éléments de base du DDMRP – méthode de planification avec des règles robustes -, que de nombreux industriels se sont approprié, et qui pourrait séduire davantage de distributeurs.
- 3 idées reçues sur les stocks – Findle
- Pourquoi en pilotage des stocks, l’analyse ABC ne suffit pas… – Findle
- Si la pénurie des semi-conducteurs était une pièce de théâtre … – Findle
- Photos: Walmart Excess Inventory Leads to Overflow at Stores, Goods in Aisles (businessinsider.com)
- Retailers’ excess inventory could mean big bargains for shoppers squeezed by inflation (nbcnews.com)