La gestion des pièces détachées de maintenance
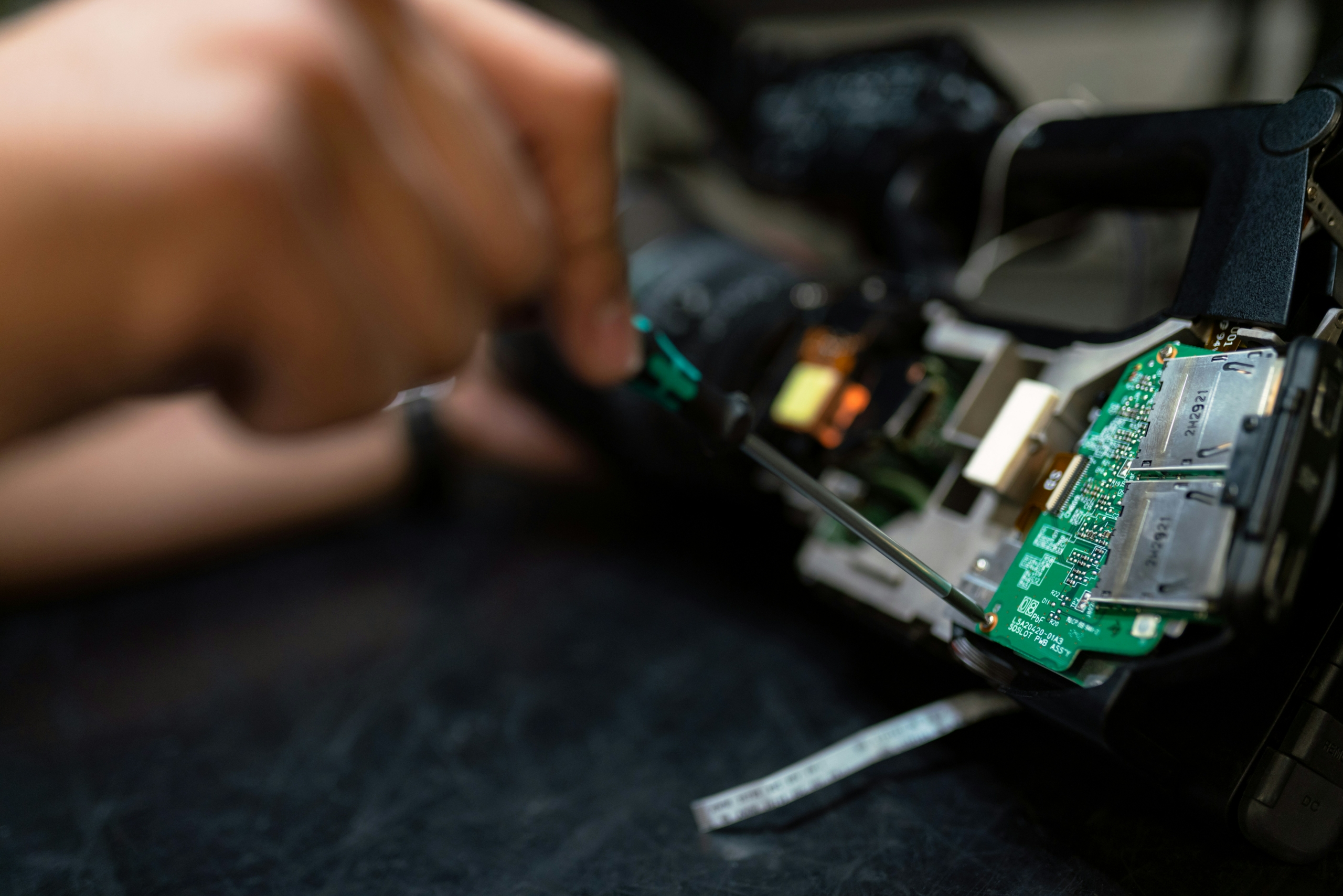
Nous avons vu dans un article précédent la gestion du stock des pièces détachées. On peut distinguer 2 grandes familles de pièces détachées. D’une part, nous retrouvons celles qui sont vendues à des clients. D’autres part, il y a la famille des pièces détachées utilisées pour la maintenance de ses propres équipements.
Dans cet article, nous parlerons de plusieurs sujets autour de ces dernières :
- 1. Comment dimensionner mes stocks ?
- 2. Comment prévoir ma consommation ?
- 3. Quels outils informatiques utiliser ?
- 4. Quelles optimisations possibles ?
Comment dimensionner mes stocks ?
Le dimensionnement des stocks de pièces détachées pour la maintenance est un sujet complexe. Comme habituellement en Supply Chain, il est nécessaire de segmenter dans plusieurs familles et d’identifier la disponibilité attendue.
On retrouvera donc plusieurs familles. Les pièces à volume relativement stable ne posent pas de problème particulier. Elles réagissent de manière classique : on peut prévoir leur consommation, la projeter et elles réagissent bien à la plupart des méthodes de pilotage.
Les pièces avec des sorties erratiques fonctionnent bien sur un MIN-MAX un peu particulier : le dimensionnement permet d’absorber toute consommation potentielle, le réapprovisionnement se faisant à la première sortie, au MOQ près.
Restent enfin les pièces avec une consommation quasi-nulle. Il faudra alors analyser les probabilités de panne, la disponibilité attendue et surtout la réactivité nécessaire. Le choix sera ensuite économique entre le coût de stockage, le coût d’arrêt et les probabilités.
Evidemment, l’équilibre entre un stockage interne ou chez le fournisseur est à prendre en compte. Le contrat de maintenance, à écrire pendant la phase de négociation de l’équipement, devra dans tous les cas bien délimiter les responsabilités du fournisseur sur le stockage de ces pièces.
Comment prévoir ma consommation ?
L’exercice de prévision n’est pas aisé dans ce domaine de la Supply Chain. Il faudra distinguer les consommations planifiées et non planifiées.
Dans les consommations planifiées, on identifiera toute la maintenance préventive, qu’elle soit pendant des maintenances annuelles ou plus routinières. Totalement prévisibles, ces consommations demandent un exercice de planification structuré ainsi que des nomenclatures de maintenance pour déclencher des besoins. Typiquement, les pièces exceptionnelles à utiliser pendant les maintenances planifiées n’ont pas forcément à être gardées en stock mais peuvent être commandées en anticipation de l’acte de maintenance.
Dans les consommations non planifiées, on retrouvera évidemment toute la maintenance pour panne / sur expertise. La prévision peut alors passer par des analyses historiques, des informations venant des fournisseurs ou d’autres utilisateurs voire d’intelligence artificielle et de machine learning.
Reste enfin une dernière catégorie, entre les deux précédentes. Il s’agit des actes d’amélioration des machines, souvent réalisés par des équipes de maintenance. Ces actes pourront alors soit piocher dans le stock disponible soit nécessiter des pièces à commander. Dans tous les cas, il est alors possible d’avoir un temps disponible entre la planification de la maintenance et la disponibilité des pièces puisque cet acte est par définition non urgent. Il faut cependant être méticuleux dans la préparation de cet acte : temps, pièces nécessaires, paramétrage et documentation notamment.
Quels outils informatiques utiliser ?
La question cruciale sur la partie informatique est dois-je utiliser ma GMAO, mon ERP ou un APS pour l’ensemble du pilotage. La réponse est : ça dépend. La GMAO aura l’avantage de lier les actes de maintenance, le planning de maintenance et les pièces en question, d’autant que la plupart possède des fonctionnalités en Supply Chain.
Les autres solutions, ERP ou APS, peuvent avoir des avantages, notamment de lier plus facilement à l’ensemble du flux transactionnel ou d’avoir des fonctionnalités avancées en pilotage de stock. L’architecture existante sera cruciale dans la décision finale.
On comprend cependant que quelque soit le système choisi, une importance particulière devra être mise sur la qualité des données. Nous pouvons en identifier 3 types : les données d’identification, les données techniques et les données financières. Parmi celles-là, la difficulté repose sur les données techniques, souvent mal renseignées (plan, matériaux, etc). La bonne pratique consiste à identifier les bonnes données à récupérer et y dédier des ressources. Enfin, attention aux entreprises qui seraient tentées de ne pas référencer l’ensemble des pièces – il est en effet parfois plus facile d’acheter rapidement une pièce sans la référencer. Cela ne paraît rien sur le moment mais crée un effet boule de neige des années ou dizaines d’années plus tard.
Quelles optimisations possibles ?
Evidemment, les optimisations dépendent de l’activité, la performance actuelle, la performance cible. Cependant, quelques sujets sont récurrents et méritent d’être étudiés :
- La remise à plat des données et référentiels. Nous l’avons déjà évoqué plus haut, mais il est primordial d’avoir l’ensemble des articles référencés avec des données associées suffisantes. Un exemple : référencer tous les achats auparavant gérés sans référence permet de négocier de meilleurs prix annuels avec les fournisseurs
- Optimiser le schéma directeur de maintenance. Dans le cas de plusieurs sites, il est possible de mutualiser sur des plateformes l’ensemble des pièces dont les rotations sont faibles pour éviter de multiplier les lieux de stockage ou de mutualiser les achats et réceptions pour les pièces avec des enjeux économiques plus importants
- Optimisation de la logistique. La logistique sur ces pièces peut parfois être un peu délaissée. En effet, le métier premier d’une maintenance est bien… la maintenance. Or, la complexité de gestion nécessite de professionnaliser la logistique. On peut penser à l’amélioration du matériel, du rangement, des compétences, des processus, des outils. Tout cela permettra d’améliorer à la fin la performance globale non seulement de la maintenance mais de l’ensemble du ou des sites.
- Etudier l’apport de nouvelles technologies. Parmi ces technologies, on pensera à l’impression 3D pour améliorer la disponibilité et le stock de la longue traine de références ou encore au machine learning pour mieux prévoir les maintenances futures et donc optimiser le stock
Et maintenant ?
Souvent complexes, les sujets de gestion des pièces détachées dans les activités de maintenance possèdent des gisements importants de valeur. Loin d’être un stock pirate au fond d’un hangar, il faut considérer cette activité à part entière avec toute la technicité nécessaire à son bon fonctionnement. Et vous, comment fonctionnez-vous ?
Redécouvrez nos articles en lien :
- Pièces détachées : 4 raisons de les distribuer – Findle
- Pièces détachées : la gestion des stocks – Findle