La consigne : d’initiatives isolées à une industrialisation du procédé ?
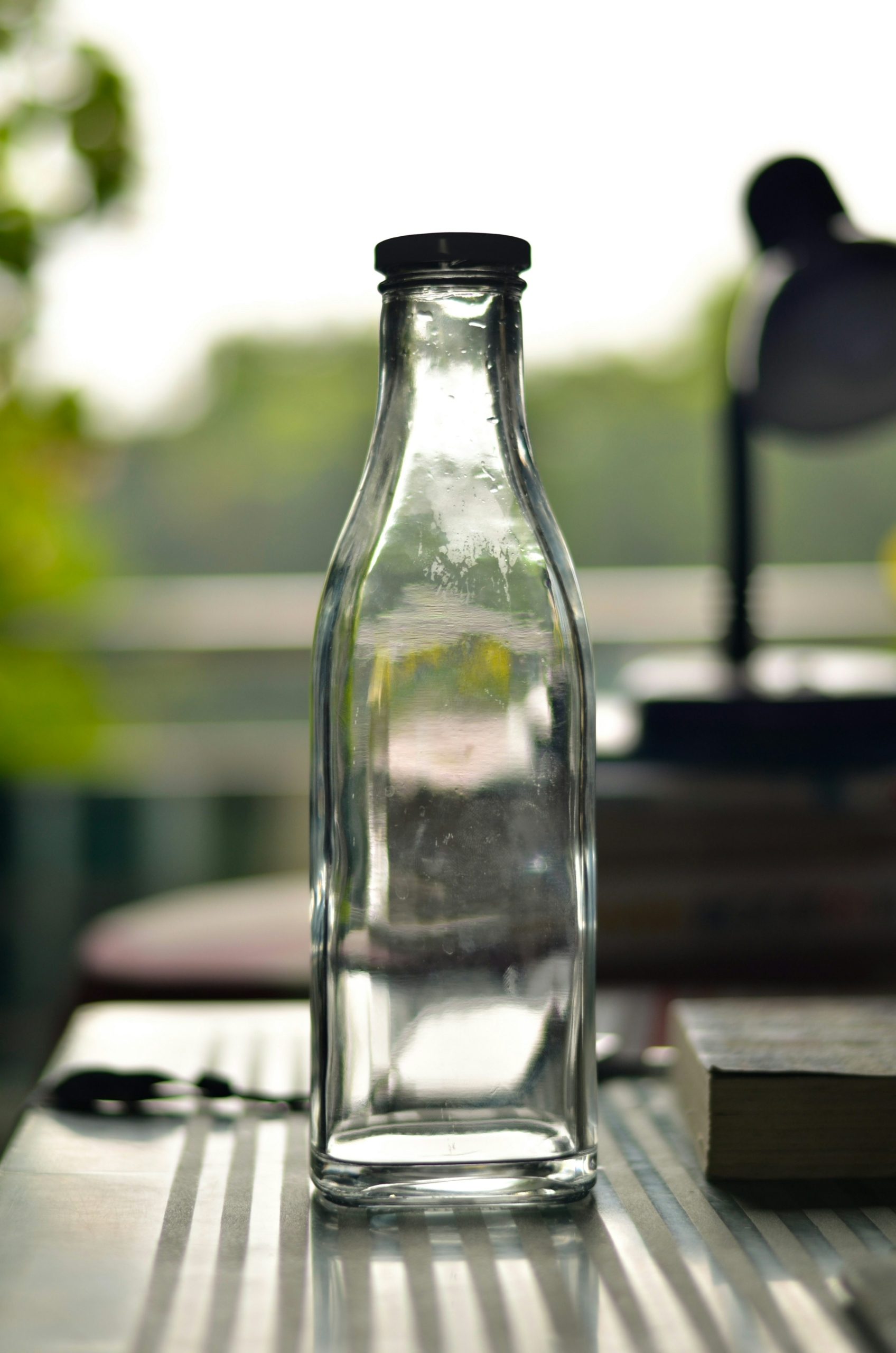
Si la consigne était une pratique courante dans les années 1960, elle s’est démodée pendant les Trente Glorieuses et l’apogée du plastique. Aujourd’hui en France, c’est seulement 10% de la production de bouteilles en verre qui est consignée. Et nous ne parlons pas des autres matières éligibles à la consigne comme le plastique, l’aluminium et même les briques en carton.
Aujourd’hui, le contexte sociétal et la montée en puissance des actions environnementales placent la problématique de gestion des emballages et des contenants au cœur du monde de la grande distribution. De plus en plus d’initiatives locales voient le jour, menées par des acteurs indépendants ou des collaborations entre start-ups et enseignes, à l’instar de Carrefour et Loop.
A l’échelle de la grande distribution, nous pensons que l’industrialisation du processus de consigne implique de réfléchir à plusieurs impacts sur l’ensemble de la chaine d’approvisionnement, parmi lesquels :
- Le traitement des articles consignés dans l’organisation logistique : ils pourront être traités au même titre que des contenants (palettes, bacs…) ou produits retournés actuels, en s’inspirant par exemple des processus de reverse. Cela implique donc la mise en place de traçabilité et gestion au sein des différents outils ainsi que de processus adaptés (le TMS pour la gestion des tournées retour voire l’évolution de l’optimiseur de tournées, le WMS pour garder une trace des mouvements de stock au sein des entrepôts mais aussi des points de vente).
- La relation et l’organisation avec les industriels qui devront également adapter leurs processus logistiques, produit et de production ainsi que leurs SI pour intégrer les consignes ; il est probable que cela ait également des impacts sur le stockage, l’implantation et les flux : par exemple, il faudra penser à intégrer des lignes de nettoyage en interne ou en externe.
- La rentabilité globale devra être étudiée. Si l’économie de l’emballage est évidente, il faut intégrer des coûts supplémentaires dans l’équation : ramassage, nettoyage, réutilisation, incentive pour le consommateur, etc.
- Le procédé de passage en caisse, pour lequel des règles devront être également définies depuis le système d’encaissement jusqu’à la remontée des stocks. Si l’on souhaite tracer les éléments, l’objectif sera donc d’identifier à la fois le produit et son contenant afin de mettre à jour le stock. Une information supplémentaire pourra être portée par l’EAN dans l’outil de gestion commerciale de manière à le lier à une typologie de contenant en fonction du produit. Le travail sur le référentiel est primordial pour la bonne mise en place du processus.
- Concernant la rétribution client (ce que gagne le client à rapporter sa consigne), le système a priori le plus simple du point de vue du distributeur consisterait à utiliser le système de fidélité existant : le client est connu, les processus sont en place et les possibilités de rétribution sont multiples et personnalisables. D’autres types de compensations pourraient être utilisées comme avantage concurrentiel (par exemple, un remboursement direct) mais nécessitent des conditions d’utilisation et un encadrement strict.
- Enfin, le suivi des transactions en consigne donnerait un axe supplémentaire d’analyse des comportements d’achat des clients et permettrait aux distributeurs d’adapter leurs services.
Ces éléments sont une première marche dans l’industrialisation du procédé de consigne à l’échelle d’un distributeur. Aussi, la massification de la pratique pourrait résulter en l’élaboration d’une stratégie multi-enseignes.
Avec des expériences reconnues dans les problématiques d’optimisation logistique et notamment en reverse, Findle serait ravi de vous accompagner dans une réflexion plus poussée sur la mise en place de processus de consigne.